Pallet Racking
Pallet Racking
-1.png?width=100&height=100&name=Untitled%20design%20(3)-1.png)
Downloads
Download the brochureOverview
Pallet racking systems consist of pre-assembled welded end frames and interlocking horizontal beams, engaging on 3” increments with safety clips for secure attachment. Complying with regulations, these systems are the foundation of warehouse racking. To enhance efficiency, integrate dynamic solutions like Pushback Racking, Pallet Flow Racking, Drive-In Racking, Carton Flow Racking, and Conveyors. Pallet racking frames come in standard depths of 24” to 72” and up to 32’ high, with custom sizes available. Pallet racking beams, in roll-formed box, welded step, or roll-formed step styles, offer capacities from 1,000 lbs. to 12,000 lbs. per pair, accommodating lengths from 24” to 192”. Accessories, including Safety Bars, Wire Mesh Decks, Row Spacers, Guards, and Hardware, ensure a comprehensive and safe pallet racking system tailored to specific application requirements.
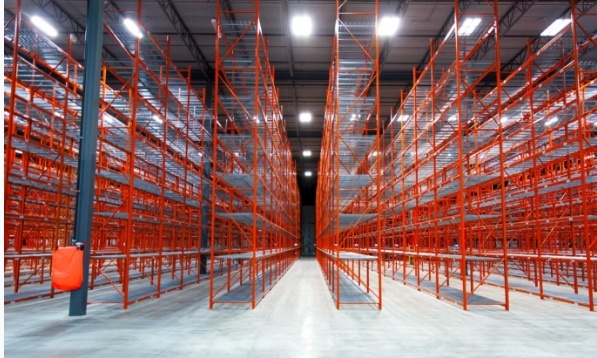
How Pallet Racking is Used:
-
Storage of Palletized Goods: Pallet racking is primarily used for the organized storage of pallets containing goods. It allows for easy accessibility and retrieval of products using forklifts or other material handling equipment.
-
FIFO Inventory Management: Pallet racking systems are often designed to follow the First-In, First-Out (FIFO) principle, ensuring that older inventory is used or shipped out first. This is crucial for industries with perishable goods or where inventory turnover is a priority.
-
Space Optimization: By utilizing vertical space, pallet racking systems help optimize warehouse space. This is especially beneficial in large facilities where floor space is valuable.
-
Ease of Handling: Pallet racking facilitates the efficient loading and unloading of goods. Forklifts can easily access pallets at various levels, streamlining the handling process
Industries that Could Benefit from Pallet Racking:
-
Retail and Distribution: Retailers and distribution centers dealing with a variety of products in palletized form benefit from the flexibility and accessibility of pallet racking.
-
Manufacturing: Industries that require the storage of raw materials, work-in-progress inventory, or finished goods often use pallet racking for efficient space utilization.
-
Food and Beverage: Warehouses dealing with food and beverage products, including perishable items, find pallet racking beneficial for FIFO inventory management and space optimization.
-
Automotive: Pallet racking is utilized in the automotive industry for the storage of parts and components, helping in the systematic organization of inventory.
-
E-commerce: With the growth of e-commerce, warehouses handling a large variety of products in bulk quantities use pallet racking to streamline order fulfillment processes.
-
Cold Storage: Industries requiring cold storage, such as frozen food distribution, often use specialized pallet racking systems designed for low-temperature environments.
-
Pharmaceuticals: Pharmaceutical companies benefit from the precise inventory control provided by pallet racking, especially when dealing with products that have specific storage requirements.
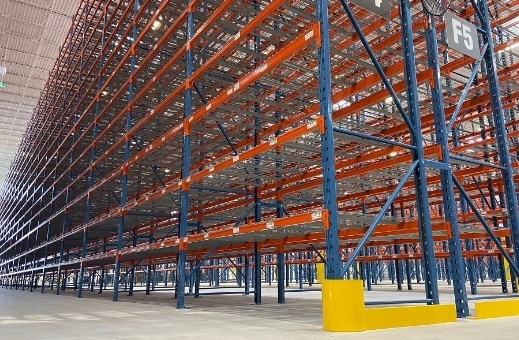
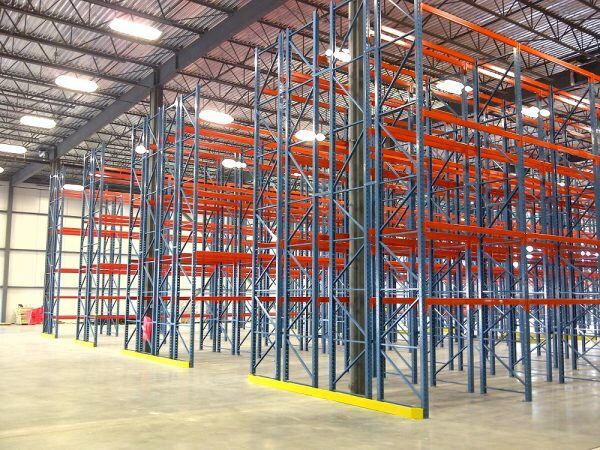
Double Deep Racking
Double Deep/Deep Reach Pallet Racking is an easy and cost effective way to increase storage capacity using standard Single Selective Racking components. Using a special Deep Reach forklift, this type of system provides two deep storage capacity and is ideal for multiple SKU applications.
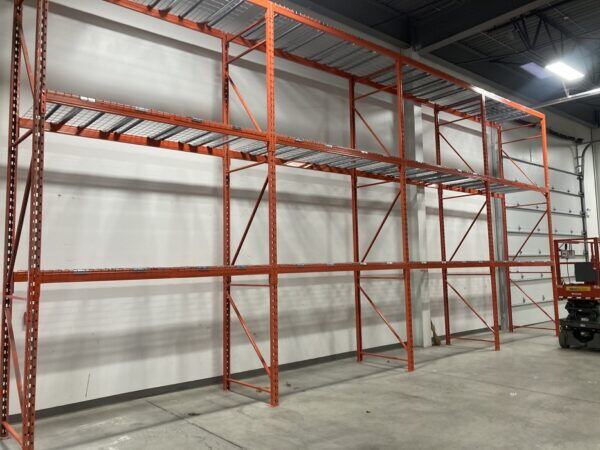
Single Selective Pallet Racking
Single Selective Pallet Racking is an economical and versatile system that can be configured for a variety of uses and product sizes when floor storage is limited. These systems provide easy accessibility to all products at all times. This type of system is commonly used throughout industry in distribution facilities for bulk storage of items. Generally the items stored on the rack are palletized.
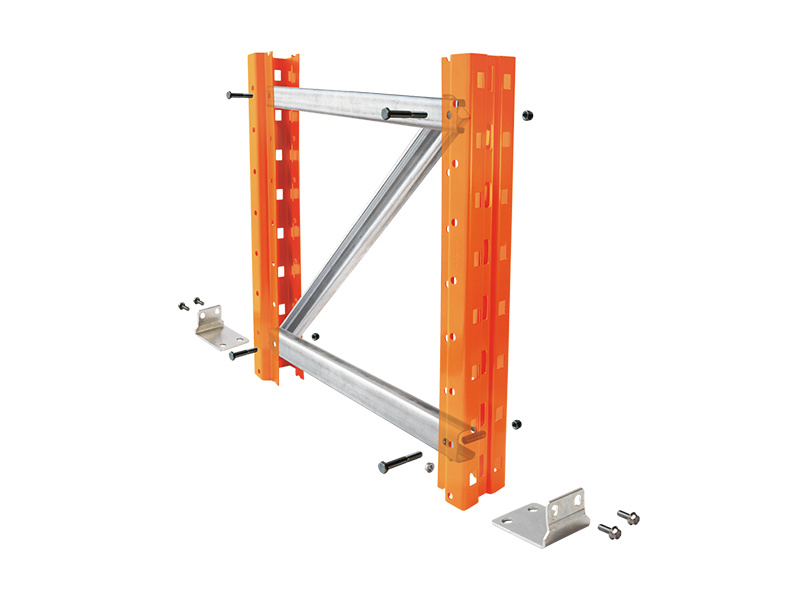
Bolted Racking
UNIRAK KD (Knock Down) is Space Aid Manufacturing’s bolted version of pallet racking that offers strength, flexibility, and cost savings over welded racking.
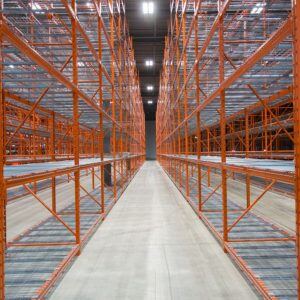
Very Narrow Aisle (VNA) Racking
Very Narrow Aisle otherwise known as VNA, is the use of Single Selective Pallet Racking in a tighter configuration to provide maximum storage density and still allows maximum selectivity. These systems typically operate in conjunction with wire-guided or rail-guided reach-truck systems. A distinct advantage of narrow aisle pallet racking is fast picking without large aisles.
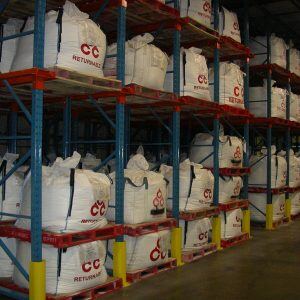
Drive-In Racking
Ideal for high density pallet storage applications, Drive-In and Drive-Thru racking are unique First In, Last Out (FILO) styles of racking that have higher storage densities than any other racking systems available. Drive-In racking allows standard fork truck access into the face of the system allowing larger storage blocks which reduces the number of required aisles. Capable of storing almost any pallet size or weight, each system must be specifically designed and analyzed by Space Aid’s Engineering Department.
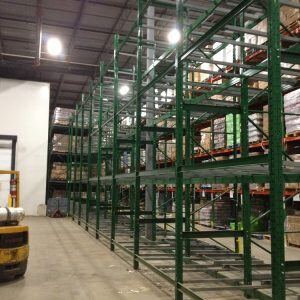
Push Back Racking
A First In, Last Out system (FILO), Push Back is designed to offer increased storage density with more pick faces than traditional high-density systems. Available in 2 to 6 deep systems Push Back is capable of handling up to 3,000 lbs. per pallet position. Standard designs are for CPC or GMA pallets, but non-standard designs for other weights, pallet sizes and containers are available. Each system is designed by Space Aid’s Engineering Department to fit your operational needs. Push Back systems require less space than Pallet Flow systems and can be arranged as back-to-back or stand alone bays.
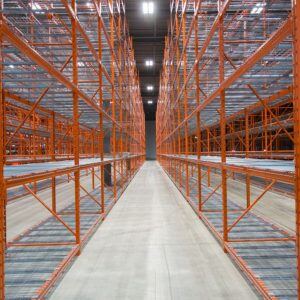
Pallet Flow Racking
Offering substantial labour and space savings over selective or Drive-In racking systems, Pallet Flow utilizes a calculated angle of descent to advance pallets along roller track or track beds from restocking position (charge) to the picking position (discharge) of the system. This First In, First Out system (FIFO) simplifies tracking and locating inventory while ensuring that product receives proper stock rotation. Each system is uniquely designed by Space Aid’s Engineering Department to fit your operational requirements. Standard systems are designed to accommodate CPC or GMA pallets, however designs are available to suit non-standard pallets and containers.
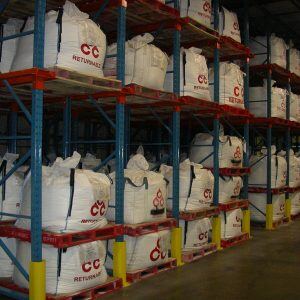
Carton Flow Racking
Ideal for both manual full carton and individual parts picking applications, Carton Flow allows product rotation on a First In, First Out basis (FIFO). Utilizing a calculated angle of descent, Carton Flow roller tracks position cartons automatically from the restocking position (charge) to the picking position (discharge) of the system allowing order pickers and assemblers uninterrupted product supply. Average design loads range from 5 lbs. to 125 lbs. per linear foot with maximum flow lengths up to 144”. Flow tracks are constructed from roll formed galvanized channels fitted with polypropylene or steel rollers on riveted steel axles. Entry and exit beams incorporate a track locating channel adjustable on 2” horizontal increments allowing easy and accurate placement of tracks and dividers.
More Solutions For You
Check out similar products that could be the perfect fit for your unique needs.
Contact Us Today
Have a project in mind? Need a few more details? Fill out the form and we will get back to you as soon as we can.